Slash Downtime During Production Testing and Keep Your Manufacturing Line Moving
In manufacturing, time is money—and nowhere is that more obvious than during production testing. Every minute of downtime means lost productivity, higher costs, and the risk of falling behind on deadlines. The good news? Downtime isn’t inevitable. With the right strategies, you can keep your testing operations smooth, steady, and on schedule.
Here’s how smart manufacturers are cutting downtime and boosting efficiency during production testing.
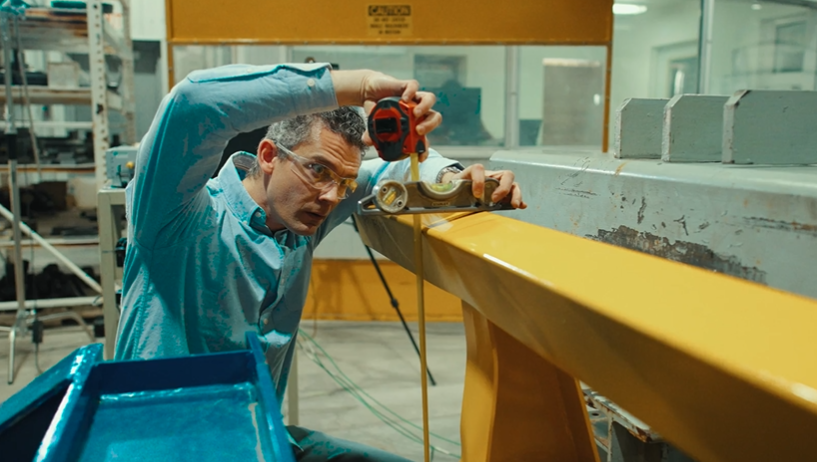
1. Start with Solid Test Planning
A little planning goes a long way. Before testing begins, map out the entire process: What are your goals? What procedures will you follow? Do you have all the equipment and resources ready to go?
When everything is clearly laid out ahead of time, you’re less likely to hit unexpected snags mid-process. It’s about being proactive instead of reactive.
2. Go Parallel, Not Sequential
Why wait when you can test more than one thing at a time? Parallel testing and multi-station setups let you run simultaneous tests across multiple products or components. That means more throughput and less time wasted. Ask, what else can we tackle while we are there? Efficient decision making saves an abundance of time.
Think of it as turning your testing operation from a one-lane road into a highway.
3. Predict Problems Before They Happen
One of the biggest downtime culprits? Equipment failure. But with predictive maintenance, you don’t have to wait for a breakdown. Using sensors and real-time data, you can spot the early warning signs of wear and tear—and fix things before they go south.
It’s like having a crystal ball for your machines.
4. Use Real-Time Monitoring and Analytics
Keep your finger on the pulse of your testing operation. With real-time monitoring and analytics, you can track performance, spot bottlenecks, and identify trends that might lead to trouble. Catching issues early keeps your process humming along.
Bonus: You get hard data to back up your continuous improvement efforts.
5. Speed Up Changeovers
If your operation requires frequent changeovers, you know how much time those transitions can eat up. The fix? Streamlined procedures.
Make sure reconfiguring equipment, updating software, and prepping new test environments is fast, efficient, and consistent. The quicker you switch gears, the less downtime you’ll see.
6. Train Your Team Like Pros
Even the best tools won’t help if your people don’t know how to use them. Skilled, confident operators can handle equipment like pros, troubleshoot issues on the fly, and keep things moving when challenges arise.
Ongoing training is an investment that pays off in fewer errors—and faster recoveries.
7. Bring in the Bots
Automation and robotics aren’t just buzzwords—they’re game-changers. Automated testing systems can run 24/7 without tiring, while robots handle repetitive tasks with precision. That frees up your human team to focus on problem-solving and innovation.
Less manual labor. More consistency. Faster turnaround.
8. Have a Plan B (and C)
Stuff happens. That’s why smart manufacturers have backup plans. Redundant systems, spare equipment, and alternative test setups ensure you can bounce back quickly if something breaks down.
It’s all about resilience—keeping your testing on track no matter what.
9. Aligning with Industry Standards
These strategies don’t just sound good—they’re in line with global standards for manufacturing efficiency, reliability, and quality. Following these practices helps you meet industry benchmarks and stay competitive in an ever-evolving market. (For Canadian standards, check out Canada.ca.)
10. Stay Ahead by Staying Efficient
Minimizing downtime during production testing isn’t just about fixing problems—it’s about building a system that prevents them. From better planning and smarter technology to investing in your people, every improvement adds up.
By making these strategies part of your standard workflow, you’re not just speeding up testing—you’re future-proofing your entire operation.
Interested in how pami can help? reach out to us, we would love to chat.